Why we invested in AtmosZero
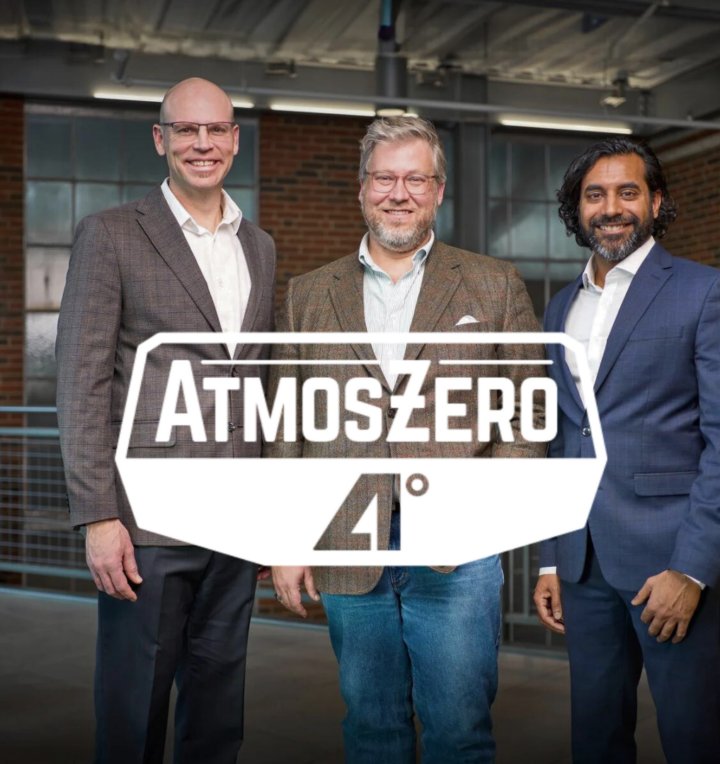
The Problem
A variety of industries require thermal energy to run their processes – ranging from food processing (sub 200°C) to rotary kilns in cement manufacturing (ca. 1,400°C). This process heat is mostly generated by burning fossil fuels like coal, oil, and natural gas in boilers, which releases an estimated 10% of global CO2 emissions (link). The combustion also causes air quality problems since it generates harmful pollutants such as sulfur dioxide (SO2), nitrogen oxides (NOx), and particulate matter (PM). Today, a solution for decarbonizing these fossil fuel powered boilers exists in the form of electric resistive systems (simply put: running electricity through metal coils which heats up the metal due to its electric resistance – similar to what’s happening in your toaster), however it has not been cost-competitive due to the higher cost of electricity compared to fossil fuels.
The Solution
AtmosZero tackles the decarbonization of heat from a different angle: by developing an electrified heat pump boiler that is capable of delivering up to 200°C temperature output – which is sufficient for a large share of required process heat including food & beverages processing, pulp & paper manufacturing, and many chemical processes. Compared to the aforementioned electric resistive boilers, AtmosZero’s heat pump is up to twice as energy efficient, making it price-competitive with natural gas boilers.
A brief explainer on the magic of heat pumps: “Heat pumps […] extract and transfer heat from one location to another in the same way that refrigerators or air conditioners do with cold — in essence, they’re air conditioners running in reverse. Because they use energy to move existing heat, heat pumps are far more energy-efficient than fossil-fired or electric-resistance boilers, which use energy to make heat directly.” (link)
While some industrial-grade heat pumps exist today, these systems tend to use waste heat as input and are customized to fit plant-specific settings which limits their broader roll-out. In contrast, AtmosZero’s technology can deliver the target output temperature using ambient air as input (with no requirement for integrating waste heat) and is designed as a robust, mass-manufacturable drop-in replacement to conventional gas boilers – and hence is suitable for the rapid decarbonization of industrial process heat.
Besides the compelling technology and large impact potential, the key reason for AENU’s investment in AtmosZero was the strong founding team composed of former ARPA-E fellows Addison Stark and Ashwin Salvi, and Todd Bandhauer, mechanical engineering professor at Colorado State University. Our confidence in the team is reaffirmed by the fact that less than 14 months after incorporation, AtmosZero last week announced its first pilot project: deploying a 650kW boiler together with Danfoss to substitute a natural gas-powered boiler at the headquarters of New Belgium Brewing in Fort Collins, Colorado.
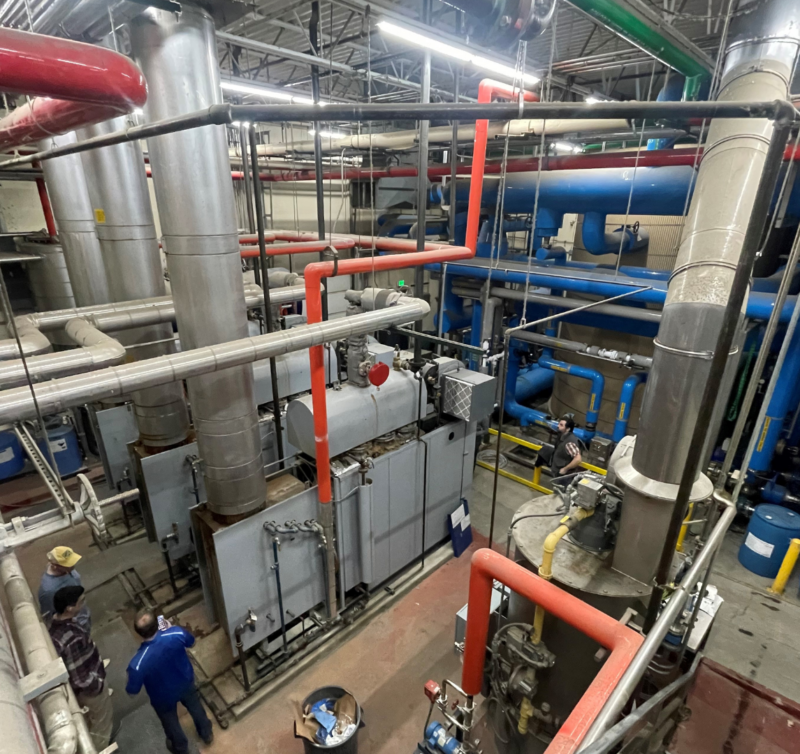
Boiler room at New Belgium Brewing
AtmosZero raised a $7.5M Seed round led by Energy Impact Partners in which AENU invested alongside Starlight Ventures.
Read the full press release here and learn how AtmosZero will decarbonize (not only) beer brewing in these articles by MIT Technology Review and Canary Media.